A state-of-the art solution that provides a suite of 3-D tools for Tank Layout, Site Planning, Job Scope, and Time Line. Utilizes Radical Software’s Artificial Intelligence Visual Analytics Tool to plan, setup and execute jobs with ease.
Planning & Setup Phase
1. Build the tank and site
- Setting up a tank takes only a few moments by entering tank dimensions and placing tank nozzles, manways and obstructions. Walls, chime, manways, nozzles, posts, floating roof supports, heaters, and sumps can all be added to form an accurate three-dimensional model of the tank.
- A simple drag-and-drop interface makes it easy to place objects. Alternatively, exact coordinates can be entered for precision placement.
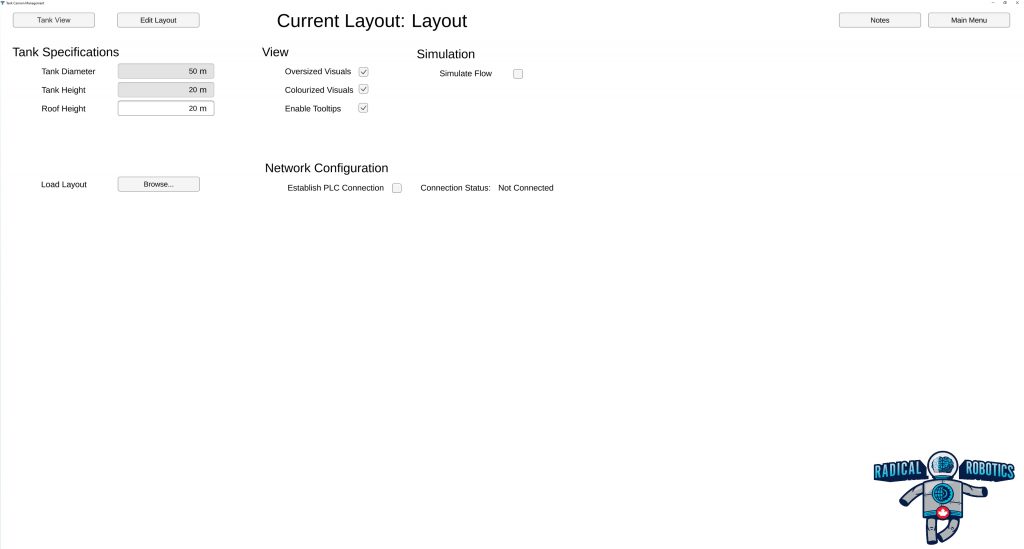
Menu Screen
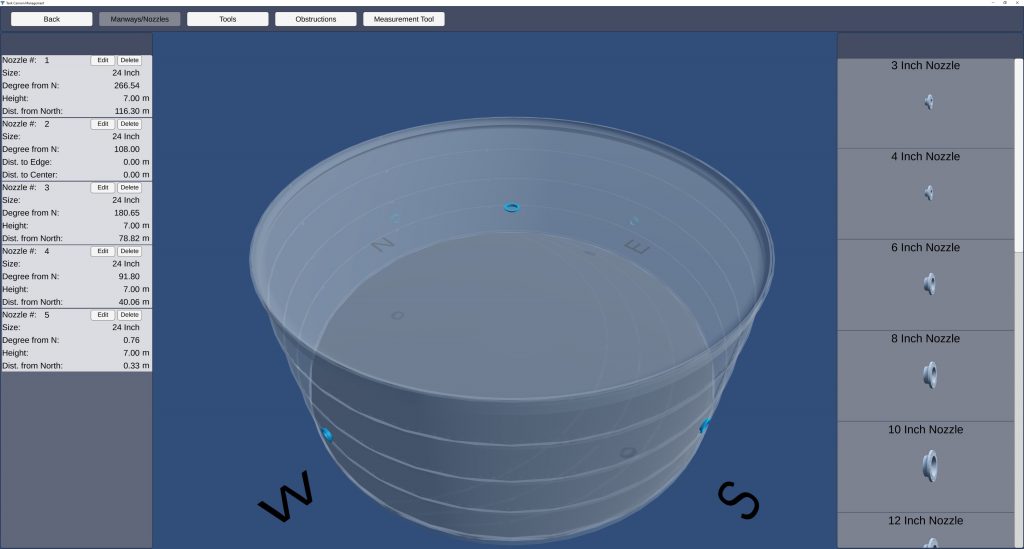
Nozzle Placement
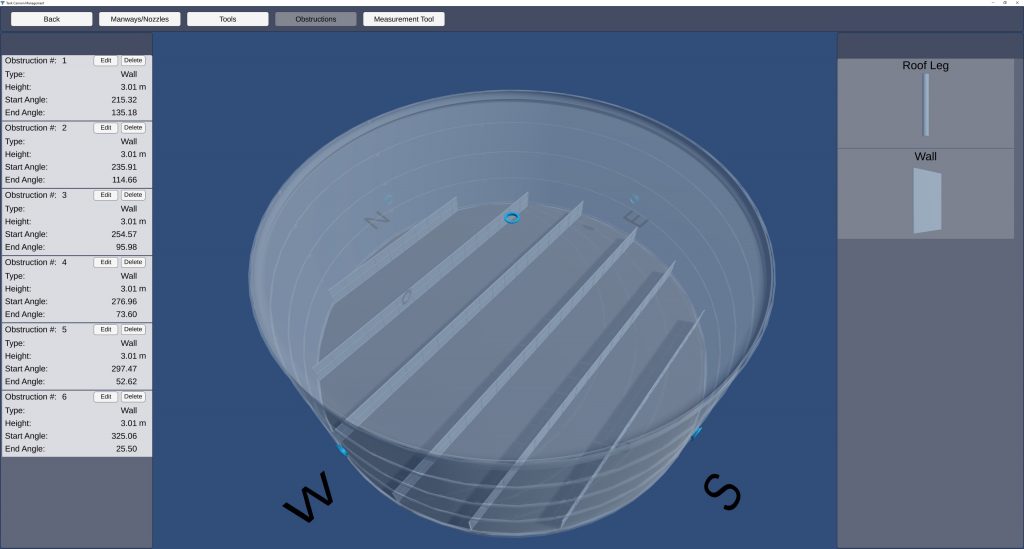
Wall Placement
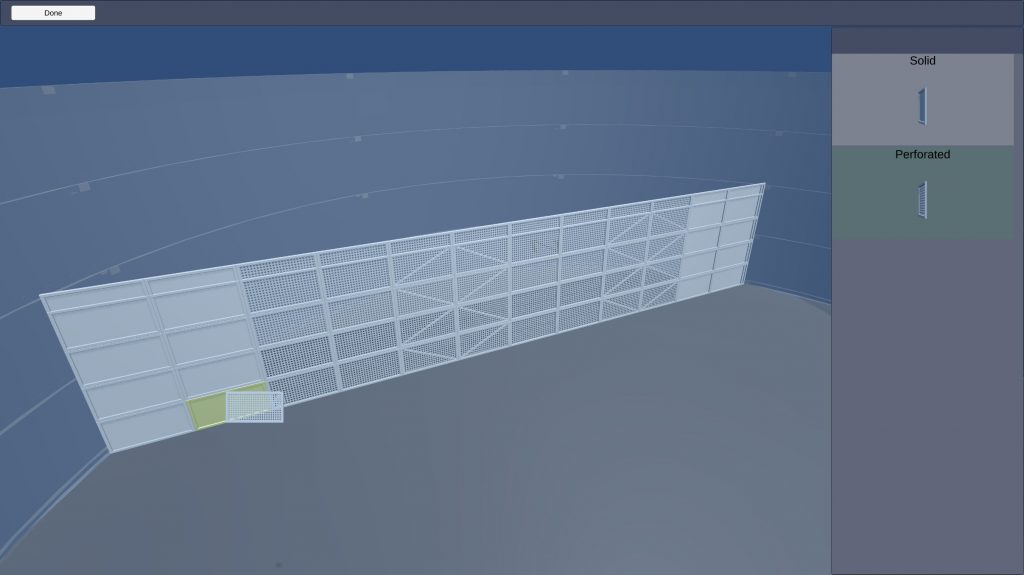
Solid or Perforated Walls
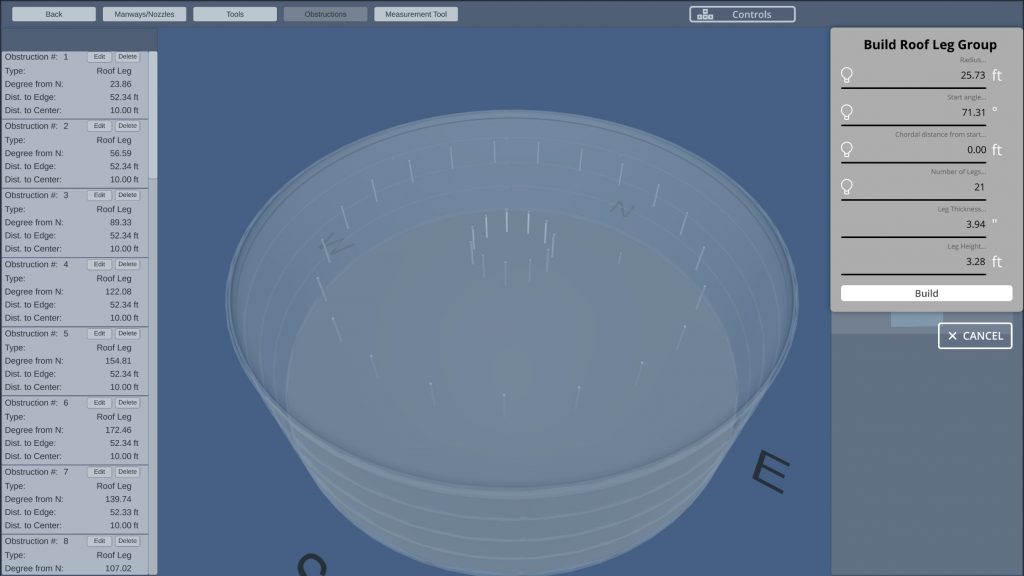
Roof Legs Setup
2. Placement of Sweeps
- Place sweeps on the nozzles. The program will add adapter flanges to inventory if required.
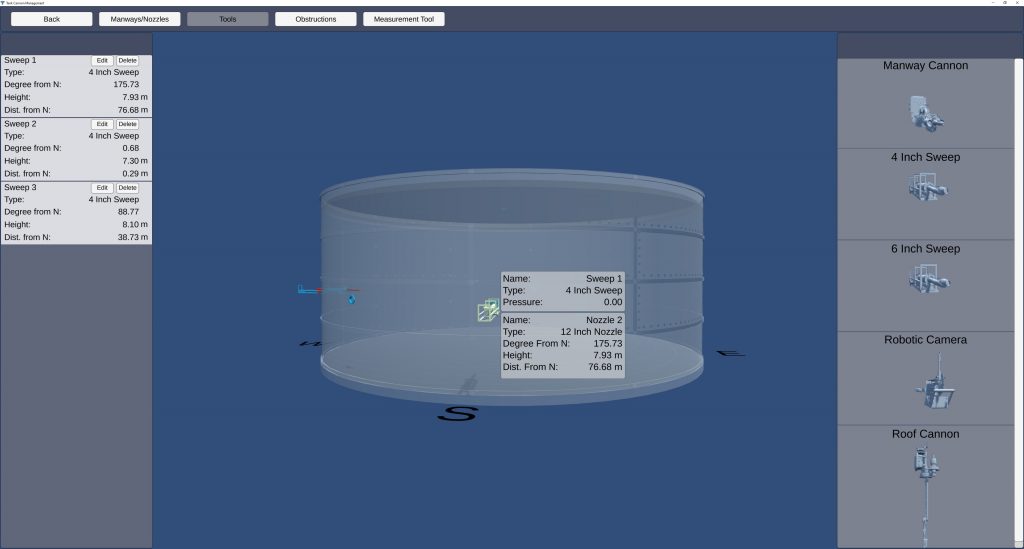
Sweep Placement
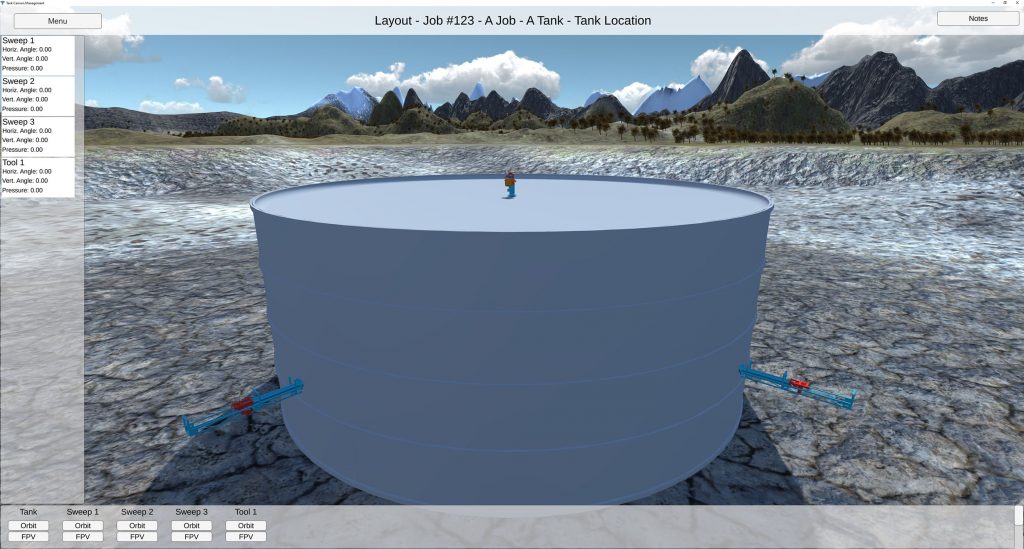
View of Sweeps on Tank
3. Sweep Simulation & Parameter Setup
- To run a simulation, the following inputs are required: fluid density, product density, solids level and desired injection flow rates.
- Adjust flow rates to determine the job’s ideal pump size for the desired time of product circulation.
- The system will determine a job schedule and provide an inventory of required components.
4. Placement of Cannons
- Cannons can now be placed in desired locations on the nozzles or manways available.
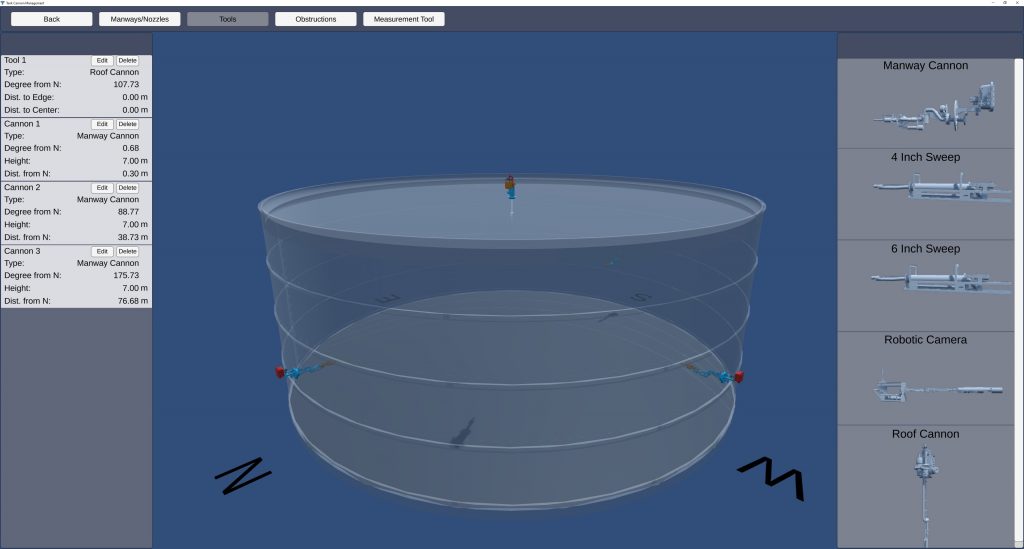
Cannon Placement
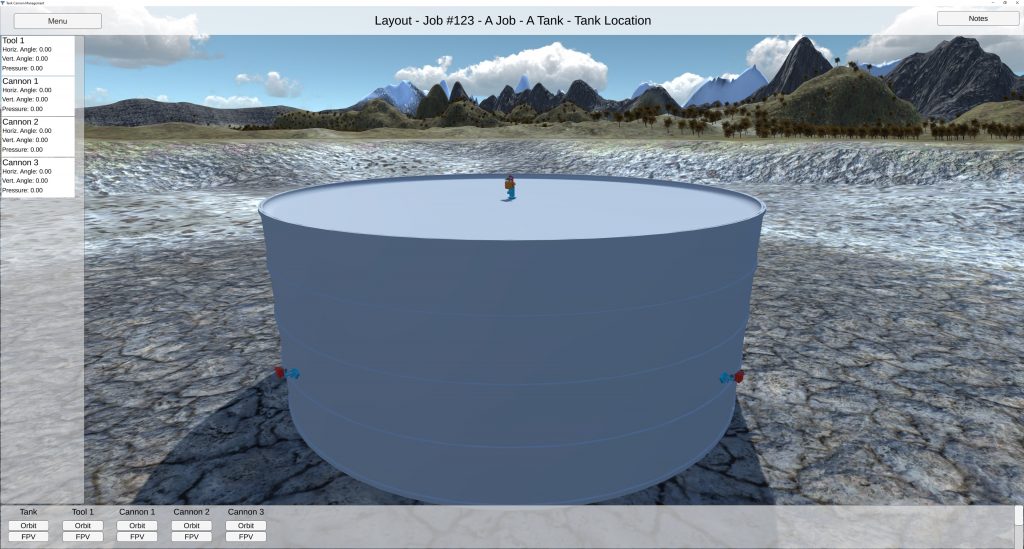
View of Cannons on Tank
5. Cannon Simulation
- The system will simulate the effective cleaning range for the configured cannons. Additional cannon placements can be setup to ensure complete tank cleaning coverage.
- The system will highlight areas of the tank that are inaccessible with the configured nozzle placements, and suggest further nozzle placements to optimize the effective cleaning capability of the selected tools.
- Program will inventory the adapter flanges needed for the job.
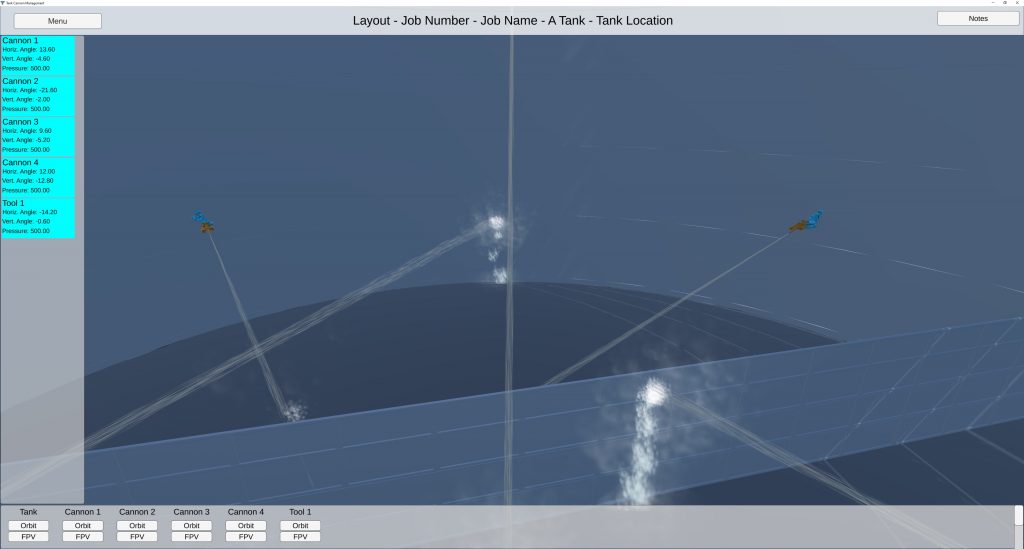
Cannon Simulation
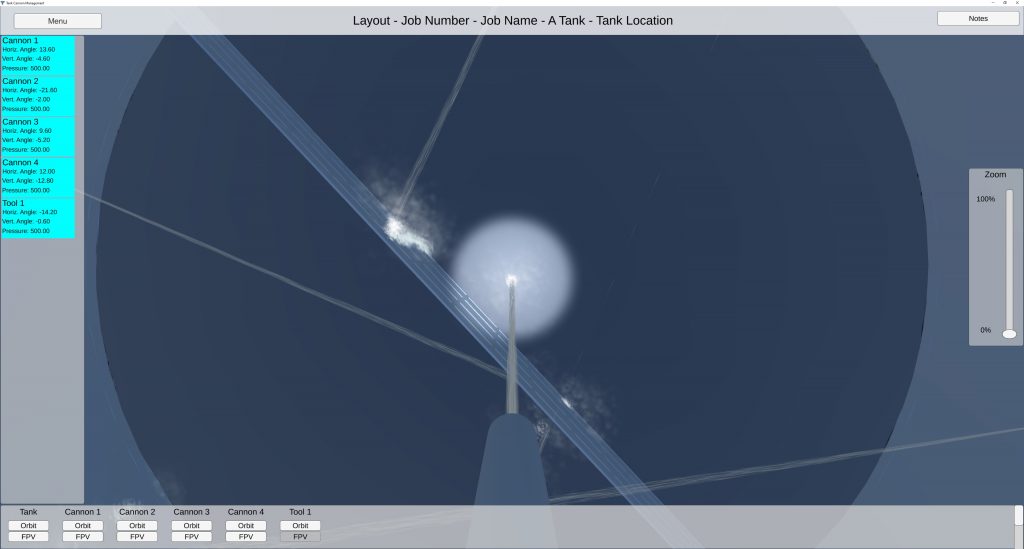
First-Person View from Roof-Mounted Cannon
Execution Phase
6. Product Circulation
- During this process it’s common to inject chemicals for the recovery of pipeline-ready oil to reduce disposal.
- Heating of the injected fluid is common to break down the product in the tank.
- Note that the sweeps are recirculating the product in the tank, suspending the solids in the fluid for extraction.
- Once released, Radical Software’s new scanning tool will provide 3D mapping of the solids and live monitoring of extraction rate with a constantly updated time to completion. This will provide a visual representation of the piles and their location in the tank.
- During this process the Circulation Management Tank (CMT) will extract the solids at a rate of 80 m3/hour.
- CMT is a fully automated circulation management system providing automated bypass when CMT is full, and tank level alerts when ready to be emptied by vac truck.
- In the event of high levels of recoverable oil from water, the CMT has a High Pressure Shearing System (HPSS) that will break down emulsions, and allow separation of the product. A seperate settling tank is required.
- The CMT can achieve oil quality of BS&W less than 1%, break emulsions, strip out sand, rock and asphaltenes, paraffin wax, and separate oil & water.
- Once sweep circulation becomes minimally effective, drain the tank and utilize cannons.
7. High Impact Blasting
- De-bulk the remaining solids with cannons.
- This process will be monitored with the cameras and lights on the cannons, along with models generated from the 3D scanning tool.
- Cannons provide a substantial impact force of 498 lbs force with 1.5 – 2 m³/min of fluid over 150 feet of range per cannon.
- Heating of the injected fluid is common to break down the product in the tank.
- During the high-impact blasting, the CMT will continue to circulate, separating the solids at a rate of 80 m3/hr.
8. Final Clean
-
Full white glove wash using a track machine for final clean.
-
We are developing an autonomous self-driving track machine that will increase the efficiency to 100% and greater compared to putting people in for final clean after de-bulk. This will be field tested and ready by 2022.
The Future of Tank Cleaning Artificial Intelligence
1. Visual Tool
Radical Software visual tool allows you to build a complete 3D site and tank layout without engineering or training with precision measurements and adjustments.
2. Cleaning Project Simulation
Radical Software Computational Fluid Dynamics Simulation allows you to simulate the cleaning and de-bulking process to find the most efficient set up and identify any hurdles prior to starting the cleaning process.
3. Scanning Tool
Radical’s soon-to-be-integrated tool allows you to see a real time 3D visual representation of the solids in the tank during cleaning. Additionally, it will adjust the erosion rate and estimated cleaning time based on actual live results during the cleaning process.
4. Artificial Intelligence
Radical Software Artificial Intelligence with live feedback will self-direct the tool operations and site management system to consistently provide maximum efficiency during the cleaning process.
Paired with our CMT/site management system, the system will trigger valves to bypass the knockout tank once it is full, which allows the system to continue to circulate while the knockout tank is emptied. A notification system alerts the site when the knockout tank is ready to be emptied.
When a vac truck is sucking out the knockout tank, the system will circulate minimal fluid from the tank circulation and agitation system to assist with moving the solids. This allows the system to never stop and suspended product to never settle.
The new autonomous self-driving tracked machine will provide comparable cleaning efficiency to manned entry without the associated risks. Utilizing the site management system and our suite of 3D scanning tools, the tracked machine will be able to avoid obstacles and plot the most effective route for optimal cleaning with no redundant passes.